Guangzhou Xinron Pharmaceutical Packaging Co., Ltd., en tant que fabricant de tubes d’aluminium médicinaux, adopte le concept de fabrication intellige
Quality is the basic foundation for the development and survival of any enterprise. To establish and maintain product quality, all company employees must be instilled with a sense of obligation and responsibility toward the concept of quality control. Each and every employee needs to demonstrate unfailing adherence to the strict PC measures that are required during the entire manufacturing process. As a leading supplier of pharmaceutical collapsible aluminum tubes and packaging materials in the pharmaceutical industry, Xinrontube makes only the most stringent demands on its employees to dedicate themselves to the strictest product quality management in the entire industry. The chief essential QC steps that comprise Xinrontube medicinal packaging tube production are as follows:
Incoming Material Inspection
Incoming material inspection refers to the assessment of raw materials, components and other products purchased from an outside source in order to confirm that they meet the standards needed, and is the first critical quality control step to occur before actual production begins. This is done by taking samples from all incoming materials and determining through testing whether or not they meet the required criteria. The importance of this first step cannot be overstated. If sub-standard material were actually to be introduced into the manufacturing process, it would result in the rejection of the entire lot and cause substantial losses both in both time and money; thereby negatively impacting the company's bottom line. The success or failure of incoming material testing not only affects the very quality of the company's final product but also influences various other direct and indirect costs. The four main areas that have a direct impact on PC inspection are - design integrity, procurement and purchase, manufacturing storage, and transportation. Indeed, these same four domains are absolutely crucial to the QC processing of incoming materials in order to ensure that only materials that meet the product criteria are actually utilized in the manufacturing process.
Production Process Quantity Control
All employees in the production department including workshop supervisors participate collectively in the exercising of quality control activities. Individuals are assigned particular responsibilities during production with each production-line member having specific duties for closely monitoring individual product. Follow-up inspections are then made by the workshop director and the QC inspector in order to prevent the flawed product from flowing on through to the next processing step. Each workshop must standardize their operations so that the product to be inspected is kept separate from the product that has passed inspection and from product found to be defective, so as not to forward non-conforming product onto the next workshop.
"5S" Management
"5S" management refers to the different tasks required to process and deliver an acceptable finished product. They include:
-
Finishing - refers to the separation of non-essential items to be marked and listed or disposed of according to need.
-
Rectification - refers to unmarked items not processed after inspection for which on-site management will determine the disposition of, accordingly.
-
Pre-cleaning - refers to the daily 10-minute maintenance activity in the operations area involving all workshop personnel prior to commencing the days' operation.
-
Post-cleaning - refers to the period immediately following shutdown during which the cleaning of the entire operations area takes place. This includes the removal of dust, dirt, debris, and other potential contaminants from all instruments, tools, and implements used in the manufacturing process as well as the sanitizing of the entire workshop area.
-
Behavioural training - refers to periodic lectures with the express intention of cultivating good manners, proper etiquette, forming good work habits, and creating discipline among employees for the purpose of promoting both a professional working environment as well as a positive corporate image.
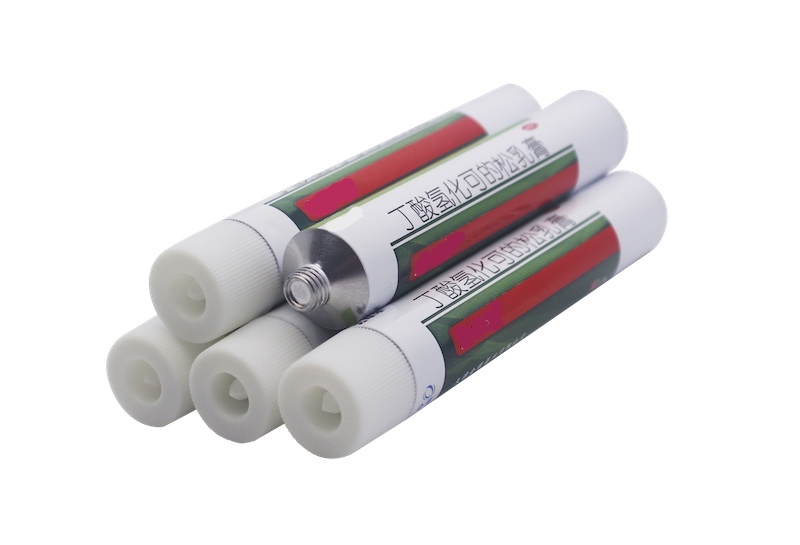
Shipping Inspection
Shipping inspection is the process of evaluating the finished product through its re-inspection using various performance tests so as to determine whether or not said product meets the needs and specifications of the intended customer. Said inspections must be performed in strict accordance with the standards and requirements set forth by the purchaser. By applying exhaustive inspections and re-inspections, a 100% satisfactory rate can be achieved.
Xinrontube strictly follows theYBB0016 2002-2015 standards for the manufacture of medicinal aluminum packaging tubes and utilizes the following test procedures to ensure standardized quality:
(1a) Approval of overall appearance and fit - This Includes the visual examination of an appropriate sample amount of the finished product in natural light to determine if the printing surface is both flat and clean and the print is clear and positioned correctly on the tube surface. Next, the aluminum tube is wiped lightly with a 30% ethanol-absorbent cloth for up to 30 times for signs of discolouration. Once the pharmaceutical aluminum tube is determined to be void of debris or foreign matter, the cap is tested by screwing it on and off the threaded nozzle ten times and then examining it under double magnification for any residual metal debris.
(1b) Approval of shape and condition of inner and outer metal surfaces. This first involves taking an appropriate sample amount of flexible adhesive coating on a rod and placing it on the end of the tube according to the specifications of the particular tube so that the rod protrudes from the nozzle making sure the pharmaceutical collapsible aluminum tube stays connected with the base during the entire test. Then, vertically applying an appropriate amount of pressure on the part of the pressure plate that protrudes and letting it gently rest on the top of the nozzle. Next, applying uniform pressure on the pressure plate and quickly squeezing the aluminum tube downward and therein determining if the medicinal aluminum tube is evenly folded and presents an "accordion" appearance. Then, after removing the pressed aluminum tube from the rod and extending it as close to the original length as possible, cutting it longitudinally in order to observe both the inner and the outer coatings for cracking or peeling.
(2) Testing the proper fitting of the pipe cap by taking a sample amount of finished product and screwing the cap on and off the nozzle twice to determine if the thread fit is precise.
(3) Testing of the tail coating for uniformity by taking an appropriate sample amount of finished product and examining it under natural light to determine if the surface of the pharmaceutical aluminum tube tail coating is consistent and sag-free.
(4) Testing for tube integrity by taking an appropriate sample amount of product with a cap screwed on in place and then immersing the tube in the water at 10-30* C at a depth of 10 mm. Then using a conical filler, applying air pressure equal to 0.2M pa to the open end of the tube in order to observe that no bubbles are emitted within 5 seconds of immersion.
(5) Testing for uniformity. Using a continuity testing machine to check the uniform integrity of the interior coating of the aluminum tube per the following SOP: When the red light on the machine panel indicates 'ON', press the verification button to establish a circuit; press the verification button continuously, and at the same time set the range accordingly. Set the selection switch to 5 mA, 50 mA or 500 mA respectively and adjust the meter so as to calibrate the pointer deflection to within 10% of 1.8 mA, 18 mA or 180 mA. Then release the calibration button thereby completing the instrument calibration process. In order to protect the meter and avoid overload, set the range selection switch to 500 mA at the beginning of the reading. Next, take an appropriate sample of the product, screw on the cap, and inject the test solution into the pharmaceutical aluminum tube at the exit point. The said test solution is created by taking 10 gms of copper sulfate, 0.05 gms of sodium succinate octanoate sulfonate, and adding 0.5 ml of glacial acetic acid to 1000 ml of water. Then, at a 10 mm mark, install the nozzle and shoulder of the aluminum tube into the V-shaped groove of the base electrode, and glide the sliding cone electrode down into the aluminum tube. Next, adjust the height of the sliding cone to make both the aluminum tube and the swing electrode coaxial. Then, press the 'test' button and determine the appropriate test range as soon as possible observing the results after 5 seconds. Do not use the same test solution for more than 8 times. Make sure the current display does not exceed 40 mA.
(6) Testing the stability of the inner coating by taking an appropriate amount of product, cutting it horizontally along the length of the tube and gently wiping back and forth across the surface of the inner coating up to 30 times with an absorbent cotton ball dipped in acetone in order to determine if the coating stays intact and continues to adhere to the inner surface of the tube.
(7) Testing the toughness requires that a finished product test sample be placed in the positioning groove of the toughness test device causing the tail end of the aluminum pipe to come into contact with the stopper to loosen the gate. When the gate falls onto the pipe body the number appearing on the scale at the top of the gate should be within the parameters listed on the table below. If the aluminum pipe is less than 16 mm, it will become necessary to add an additional plate on.
Table 1 - Toughness test limits measured in millimetres. The outside diameter should not exceed the following values:
(unit=mm)
Diameter | No exceed than the value below |
16 mm | 6 |
19 mm | 8 |
22 mm | 10 |
|
(8) Testing microbiological limits. Using 10 pieces of the finished product, add sodium chloride solution to two-thirds of the indicated capacity, and shake for 1 minute to obtain the test solution. After the membrane of the test solution is filtered, check it according to published regulations found in Chinese Pharmacopoeia 2015 edition Four General Rules 1105 &1106, to ensure the number of bacteria does not exceed 100 CFU per branch; and that the number of moulds or yeasts do not exceed 100 CFU; and lastly by microscopic observation, that neither Staphylococcus aureus nor Pseudomonas aeruginosa is detectable.
(9) Testing to determine that the product is aseptically acceptable. This is done by taking 11 units of finished product and adding a sodium chloride solution with a labelled volume of one-half, then shaking for 1 minute and combining the extracts to determine if they comply with the standards as expressed in the Chinese Pharmacopoeia, 2015 edition, Four General Rules 1101. This test is applicable for squeezable ointment tubes used in surgery, or for burns, or in severe trauma cases.
(10) Testings for abnormal toxicity. This requires taking 5 pieces of finished product and adding a sodium chloride solution of a pre-indicated strength and shaking for 5 minutes. Then combining the extracts for backup, intravenous injection and finally checking to ensure the results comply with the Chinese Pharmacopoeia, 2015 edition, Four General Rules 1141.
(11) Testing for primary skin irritation. This requires taking 5 pieces of the finished product, adding a sodium chloride solution with an indicated strength, shaking for 5 minutes, combining the extracts for later use, and monitoring in accordance with the skin irritation test (YBB00072003 -15. The test should show no irritant response.
An International Invitation
Guangzhou Xinrontube Pharmaceutical Packaging Co., Ltd. is a major Chinese manufacturer of medicinal collapsible aluminum tubes and is recognized as a world leader in the industry through its relentless efforts to set the industry standards. As such, GXPPC invites you to join hands in helping to make our global environment a safer and better place to live through mutual cooperation and understanding.



